In the world of packaging, flow pack machines play a crucial role in ensuring efficient and speedy wrapping of products. However, downtime in these machines can significantly impact productivity and ultimately, the bottom line. In this comprehensive guide, we will explore the top ten strategies to reduce downtime in your flow pack machine, helping you optimize your operations and maintain a competitive edge in the market.
1. Regular Maintenance and Inspection
A proactive approach to maintenance and inspection is essential in minimizing downtime. Scheduling routine checkups for your flow pack machine will help identify potential issues before they escalate. This includes examining parts such as the sealing jaws, cutting knives, and conveyor belts, as well as verifying the proper functioning of sensors and control systems.
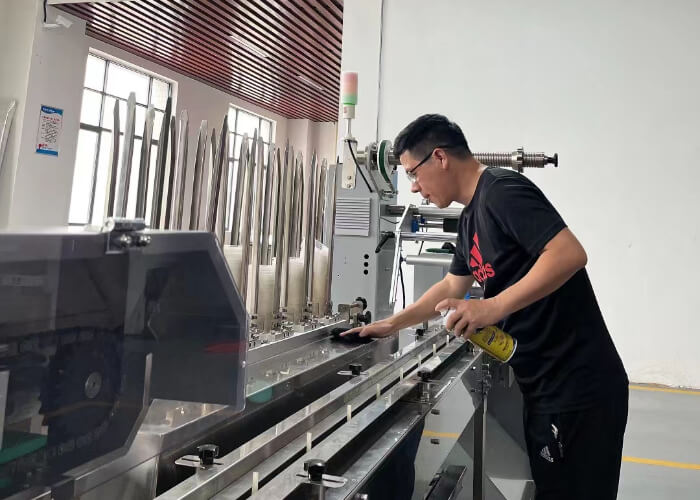
2. Choosing Quality Spare Parts
Investing in high-quality spare parts is crucial for the long-term performance of your flow pack machine. Opt for original equipment manufacturer (OEM) parts, as these are specifically designed for your machine, ensuring optimal performance and compatibility. In turn, this will decrease the likelihood of breakdowns and reduce downtime.
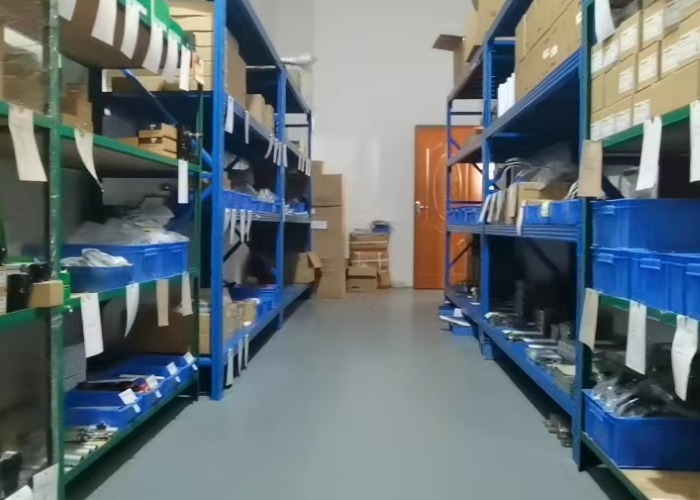
3. Implementing Predictive Maintenance
Predictive maintenance involves using data analytics and machine learning algorithms to anticipate equipment failures before they occur. By analyzing performance trends and patterns, you can identify potential issues and schedule maintenance accordingly, preventing unplanned downtime and increasing overall efficiency.
4. Operator Training and Education
A well-trained operator is essential for the smooth functioning of your flow pack machine. Ensure that operators are educated on proper machine use, troubleshooting, and maintenance procedures. Regular training sessions can help keep your team up-to-date on best practices and contribute to reducing downtime.
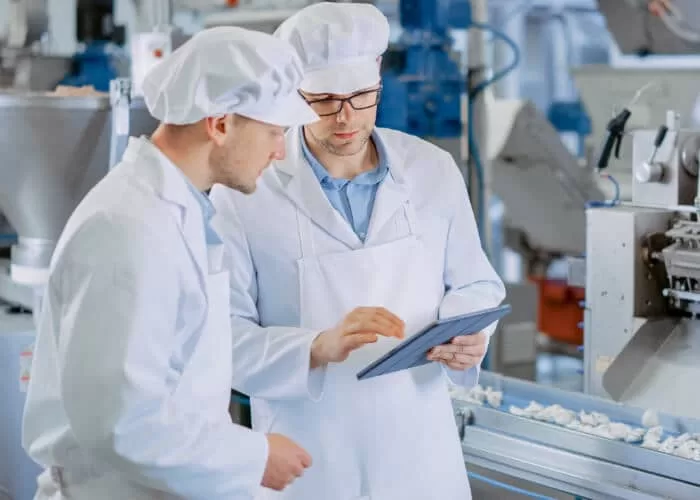
5. Keeping a Clean and Organized Workspace
A clean and organized workspace promotes efficiency, reducing the likelihood of errors and accidents. Ensure that your flow pack machine is kept clean and free of debris. This not only helps in maintaining the machine’s performance but also makes it easier to identify and resolve potential issues.
6. Timely Software Updates
Flow pack machines rely on sophisticated software to operate efficiently. Regularly updating the machine’s software ensures that it runs on the most current version, optimizing performance and minimizing the risk of downtime caused by outdated or malfunctioning software.
7. Streamlining Changeovers
Frequent product changeovers can lead to significant downtime. Streamlining these processes by utilizing quick-change tooling and adopting efficient setup procedures can minimize the time spent on changeovers, ultimately reducing downtime.
8. Opting for Modular Design
A modular design allows for easy access to critical components, facilitating swift maintenance and repair. By choosing a flow pack machine with a modular design, you can minimize the time spent on troubleshooting and maintenance, reducing downtime and enhancing productivity.
9. Establishing a Preventive Maintenance Schedule
Creating a preventive maintenance schedule is essential for keeping your flow pack machine in optimal condition. This schedule should outline routine tasks such as lubrication, cleaning, and inspection, as well as when to replace wear parts. Adhering to this schedule will help prevent unexpected downtime.
10. Monitoring Machine Performance
Regularly monitoring your flow pack machine’s performance can provide valuable insights into its overall health. Tracking key performance indicators (KPIs) such as machine uptime, production rates, and product quality can help you identify areas that require improvement and ensure that your machine is operating at its full potential.
Conclusion
Reducing downtime in your flow pack machine is crucial for maintaining productivity and staying competitive in the packaging industry. By implementing strategies such as regular maintenance, investing in quality spare parts, streamlining changeovers, and monitoring performance, you can significantly decrease downtime and optimize your operations.