Flowpack machine is widely used in many industries today. And more and more customers are buying machines from China flowpack machine manufacturers.
Customers are very far away from the manufacturer, Thus the factory acceptance test (FAT) is very super important to ensure the manufacturer will deliver a reliable flowpack machine.
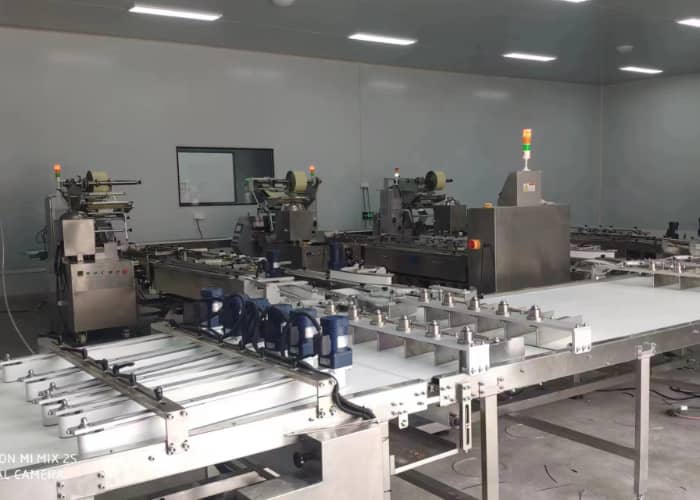
By conducting FAT, it ensures the functionality, reliability, and performance of the flow pack machine before the installation and commissioning on the customer site.
And in this article, we will guide you to look into the FAT process, its benefits, and the important steps you should follow.
Approaches for conducting a Factory Acceptance Test (FAT) for flowpack machines:
- On-site Inspection: Visit the manufacturer in person. Observe the machine’s operation, test its functionality, and solve any concerns immediately.
- Third-Party Inspection: Appoint a third-party inspection company. Their experts have the necessary knowledge and experience to evaluate the machine’s performance, verify compliance with specifications, and provide an unbiased assessment.
- Online Video Conference Acceptance: Ask your manufacturer to make the trial test, To check the machine’s operation remotely.
Important steps involved in a Factory Acceptance Test (FAT) for flowpack machines:
- Verify machine dimensions: Firstly check if the machine’s overall size matches the specifications and drawings to ensure there is no problem for onsite accurate installation.
- Inspect electrical configuration: Verify the components brand, parameters, make sure correct components were well installed in the machine.
- Perform packaging material test: Install an appropriate-sized packaging film and do the trail tests with similar products to evaluate packaging speed, seal quality etc.
- Packaging Material Testing: If you are going to use different type of packaging material on your flow pack machine, be sure to verify the compatibility of the machine with different types of packaging materials, such as PE foils, or laminates. Test the machine’s ability to handle various material thicknesses and ensure proper sealing performance.
- Integration Testing: If your flowpack machine is part of a larger production line, conduct integration tests to ensure seamless communication and synchronization with other machines.
- Long-Term Performance Testing: Run the flowpack machine continuously for an extended period to assess its performance, durability, and reliability under sustained operation.
- Labeling and Printing Testing: If the flowpack machine includes labeling or printing capabilities, conduct tests to ensure accurate placement, legibility, and adherence of labels or prints on the packaging.
Benefits of Factory Acceptance Testing (FAT) for flowpack machines:
- Ensures accurate installation: By carefully checking machine dimensions, It can ensure that the machine will be fittable when installed in a designated space.
- Guarantees reliable electrical configuration: Inspecting the electrical components ensures that the machine is equipped with the correct and high-quality components.
- Enhances packaging material compatibility: Ensures that the machine can handle various types and thicknesses of packaging materials, and make sure of a smooth transition when switching to different product SKUs.
- Smooth integration with other equipment: Verify if the flowpack machine can seamlessly synchronize with upstream or downstream machines in the production line, optimizing overall productivity.
- Assures long-term performance: Through long-term performance testing, customers can identify any potential issues in the machine, allowing them to make necessary improvements for sustained operation.
Conclusion:
In summary, the Factory Acceptance Test (FAT) is a really important step when it comes to delivering a flowpack machine that works well and meets the customer’s needs.
It involves checking things like the machine’s size, electrical setup, and how it handles different packaging materials.
The FAT process helps to identify any problems and make sure the machine performs as expected. It’s all about making sure the customer is happy and that the machine works reliably.